High Current Heavy Copper PCBs
Printed circuit boards (PCBs) can come in many varieties, with one of those being high current PCBs, also called heavy copper PCBs. These units have some useful characteristics for applications with high currents and variable temperatures. Heavy copper PCBs can resist higher temperatures for longer periods while handling higher rates of electrical current and providing stronger connection points.
Here at MCL, we supply high current PCBs with heavy copper components ranging from 3 ounces per square foot (oz/ft2) to 10 oz/ft2 and can help you with extreme copper PCBs if you need higher copper concentrations. See what these PCBs can do and why you may want to use them.
What Is a High Current PCB?
As the name implies, high current PCBs can support higher critical current densities than standard boards, which might only support amperes in the double digits. High current PCBs can carry hundreds or thousands of amps and can resist higher temperatures for extended periods. As such, they provide strong connection points. The unique design of these PCBs features a thicker, heavier layer of copper that gives the PCB its durable characteristics.
Get Pricing and Lead Time Call 717-558-5975
What Is a Heavy Copper PCB?
A heavy copper PCB is a type of high current PCB with 3 oz of copper or more in the external and internal layers of the board. Even if the total amount of copper is less than 3 oz, if a PCB’s copper thickness is greater than 4 oz per ft2, it’s also considered a heavy copper PCB. An extreme copper PCB usually has 10 oz per ft2 or greater.
This heavy amount of copper is used as an alternative to adding thickness to a trace, which is not always viable. A standard PCB trace for a DC motor typically needs a specific width to deliver the appropriate power levels with consideration for thermal constraints. Heavy copper PCBs use thicker traces to do the same job with reduced width.
PCBs with heavy copper circuits can have increased thickness in the plated holes and via sidewalls. The manufacturing process is a bit different than it is for standard PCBs, with special plating and etching techniques that accommodate the copper’s additional thickness. A heavy copper PCB stands up well to high temperatures, such as welding heat, and to corrosive environments. In these instances, the copper PCB can form a non-toxic passivation layer that protects it.
Benefits of High Current Heavy Copper PCBs
The primary benefit of a heavy copper PCB is its ability to support high currents, elevated temperatures and recurring thermal cycling. These factors would normally cause problems for a standard circuit board. Other advantages of heavy copper PCBs include their:
- Structure: With heavy copper, the boards can achieve higher density and minimize the number of layers for a simple yet durable structure. They’re able to fit in more current-conducting material in a smaller space and achieve stronger mechanical strength for connectors.
- Smaller failure rate: High currents combined with increased design complexity generate more heat. With the right design, copper’s high heat conduction allows it to pull heat away from the temperature-sensitive components of the PCB, keeping them in better condition.
- Cost-effective production: Copper as a material is a little pricier, but the overall cost of production for heavy copper PCBs is reduced. A heavy copper PCB can be used in place of copper cables, which improves cost-effectiveness. Specific production methods also allow heavy copper to be mixed with standard features on a PCB, which allows for fewer layers, a smaller footprint and production cost savings.
Design Considerations and Tips
When it comes to designing heavy copper PCBs, you have some options. Generally, these boards are made in single-sided, double-sided or multilayer configurations, with single-sided and double-sided versions being the most basic and practical options. These simple configurations are good for making production more cost-effective compared to multilayer heavy copper PCBs. However, due to differences in manufacturing processes heavy copper PCBs make board construction a little more challenging and standard FR4 PCBs.
More layers, which are often necessary to handle high current loads and multiple functions, add complexity. Some things to keep in mind when designing a high current PCB include:
- The location of sensitive components: Since the higher current generates more heat, you’ll need to protect sensitive components by thermally isolating them.
- The length of the current traces: The longer the trace, the more resistance and the greater the power loss and heat generation. Keep traces as short as possible to keep the board in good condition.
- Advanced etching techniques: Standard etching techniques don’t work on heavy copper and can produce over-etching in the margins and uneven edges. To achieve straight edges and good margins, you’ll need to find a PCB supplier that incorporates the right plating and etching techniques.
- The addition of copper bars: If your application requires amps in the triple digits, traces won’t be as useful. Solderable copper bus bars can provide support for much larger currents.
- Substrate materials: Substrate materials can vary widely and must be appropriate for the higher heat of heavy copper boards. You’ll also need to factor in the relationship of thermal expansion between copper and the substrate to avoid cracking and stress on the substrate.
- Copper resistance: Electroplating can create a thicker board surface, which reduces the resistance of the copper traces and improves heat conduction and, by extension, dissipation methods.
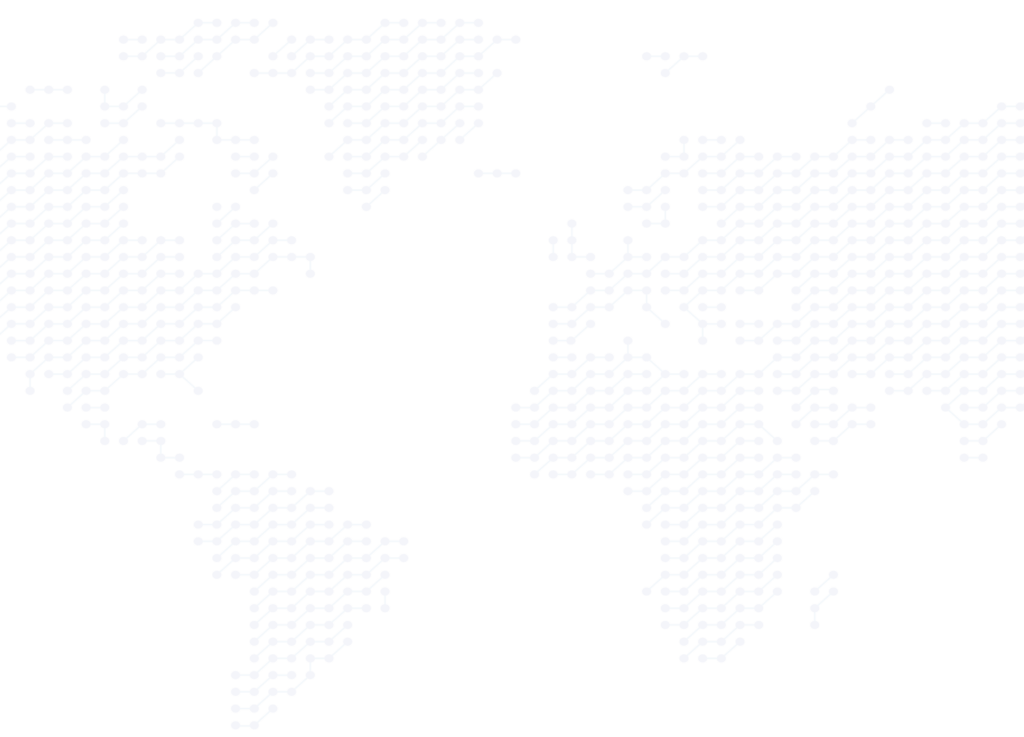
Find Out More.
Get a Free Quick Quote.

Choose Millennium Circuits Limited (MCL) for Your PCBs
High current PCBs are a core component of many devices and industries. If you need heavy copper boards for your project, MCL can help. We’re a trusted bare PCB supplier and we’ve had an ISO 9001 certification since 2014. Our knowledgeable team is ready to help you find the right circuit board for your unique application and offer exceptional customer service.
Get the benefits of selecting an established PCB supplier with the know-how to tackle heavy copper configurations at cost-effective prices. Get in touch with MCL today online or at 717-558-5975.
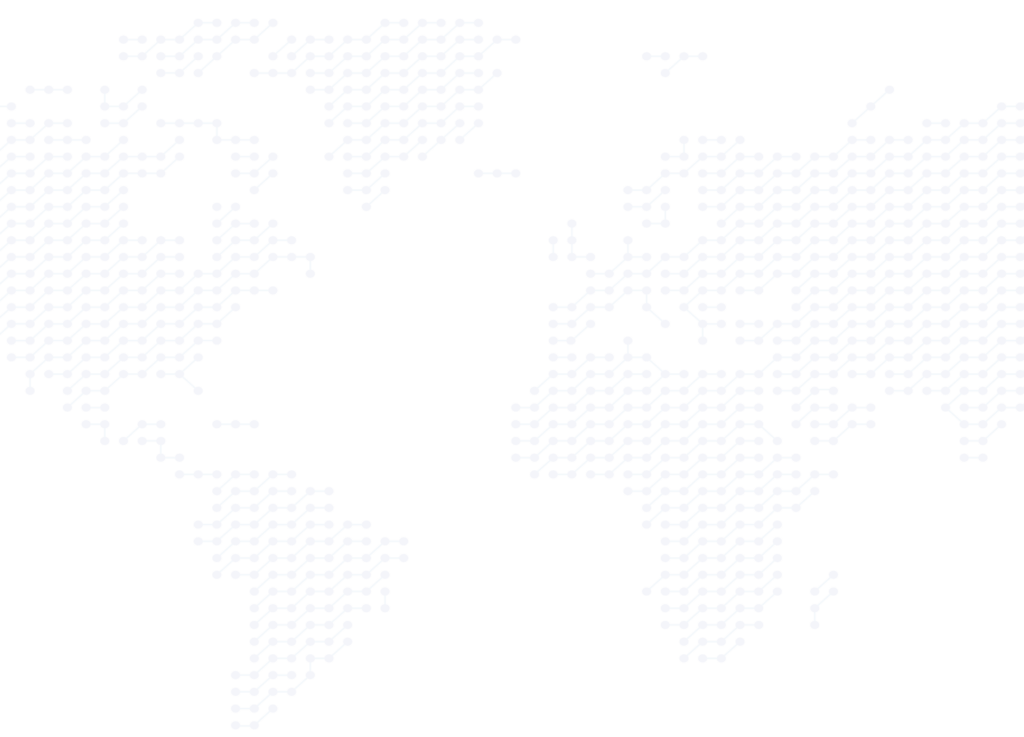
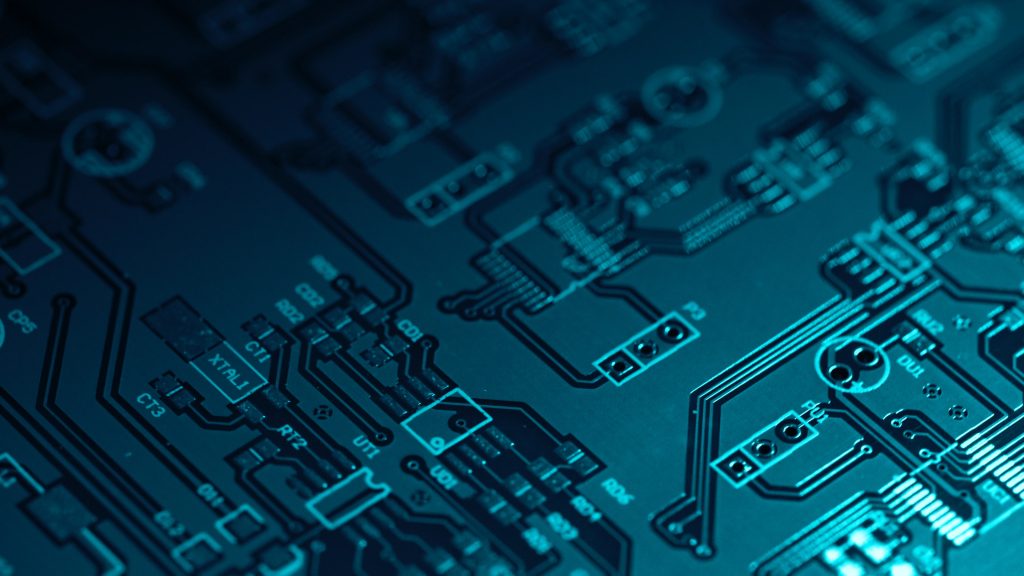
Industries Served
High current PCB clients include a wide range of manufacturers working with equipment or devices that need a lot of power. These might include essential components in an airplane, power converters and heavy machinery. Over the years, our clients have included high current PCBs when manufacturing products for industries such as:
- Automotive
- Electronics
- Industrial equipment
- Aerospace and aviation
- Solar energy
Industrial Applications
PCBs using heavy copper are critical for working with high current loads. They’re common in applications such as:
- Solar power converters
- Power regulator excitation systems
- High-power rectifiers
- Protection relays
- Nuclear power
- Traction converters for railways
- Overload relays
- Heating, ventilation and air conditioning (HVAC) systems